Plastics, films & packaging
Decisive for product quality
Roll coatings are crucial in meeting the increasing demands of ever higher quality and more sensitive products. In addition to established standard solutions for the industry, MITEX offers special coatings and individual adaptations to the requirements of each customer to guarantee the highest possible performance. MITEX roll coatings make a significant contribution to increasing product quality and process efficiency and demonstrably create measurable added value for OEMs and end users.
Our rollers solve problems with:
Causes
- Deposit of entrained adhesive mist
- Roll surface not sufficiently anti-adhesive
- Roll surface cannot be sufficiently cleaned
Effects
- Adhesive buildup on roll coating
- Impression roll is damaged at the edge of the product web
- This restricts the working widths that are possible in the future
During adhesive application, adhesive mist is carried from the application unit to the laminating unit. Adhesive residue / adhesive mist remains on the roller surface of the laminating press outside the web width. The tackiness of the deposited adhesive mist increases over time. As a result, tiny pieces tear out of the coating of the impression roller. This effect increases over time. Wider products can no longer be run.
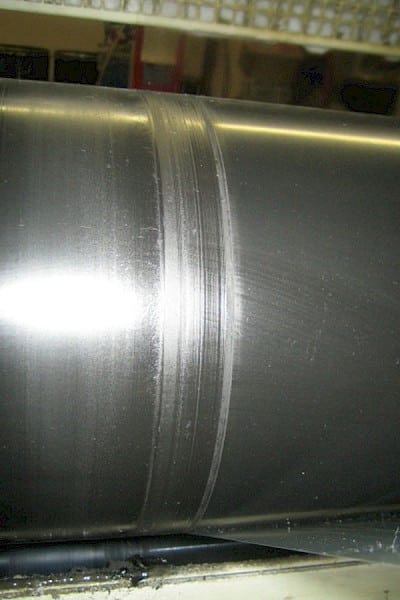
Our solution for problems with adhesions in the adhesive lamination
Causes
- Non-uniform matting / roughness of the front or back sides of films
- Inhomogeneous optical properties of foils
- Incorrect roughness for the bonding of the foils
Effects
- Lower product quality
- Visually recognizable inhomogeneities
- Streaking and spots
- Product rejects
- No process reliability
Films used in optical applications, e.g. as screen or cell phone surfaces, only allow inhomogeneities that can no longer be resolved by the human eye.
Technical films that are bonded over the entire surface of consumer electronics devices, for example, require absolutely homogeneous and precisely defined back embossing.
The uniformity of the embossing enables ideal adhesive application and thus homogeneous strong adhesion. Even on the reverse side, only those inhomogeneities that can be resolved by the human eye are impermissible, since the matt structure of the reverse side is formed through to the front side.
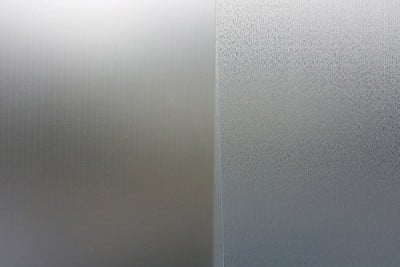
Our solution for insufficient film matting
Causes
- Wrinkling due to uneven web run
- Insufficient spreading effect
- Lamella spreader roller in use
- Uneven film thickness
- Fluctuating web tension
Effects
- Damage to the product
- Scrap production
- Wrinkles due to overstretching of the substrate
- Insufficient web guiding
Thin films in particular tend to wrinkle when beeing processed which can lead to defects and rejects in subsequent steps. The cause can be, among other things, uneven film thickness or fluctuating web tension. Traditional sheet or lamella spreaders can lead to overstretching in the center of the web or marks on the film in the case of sensitive substrates.
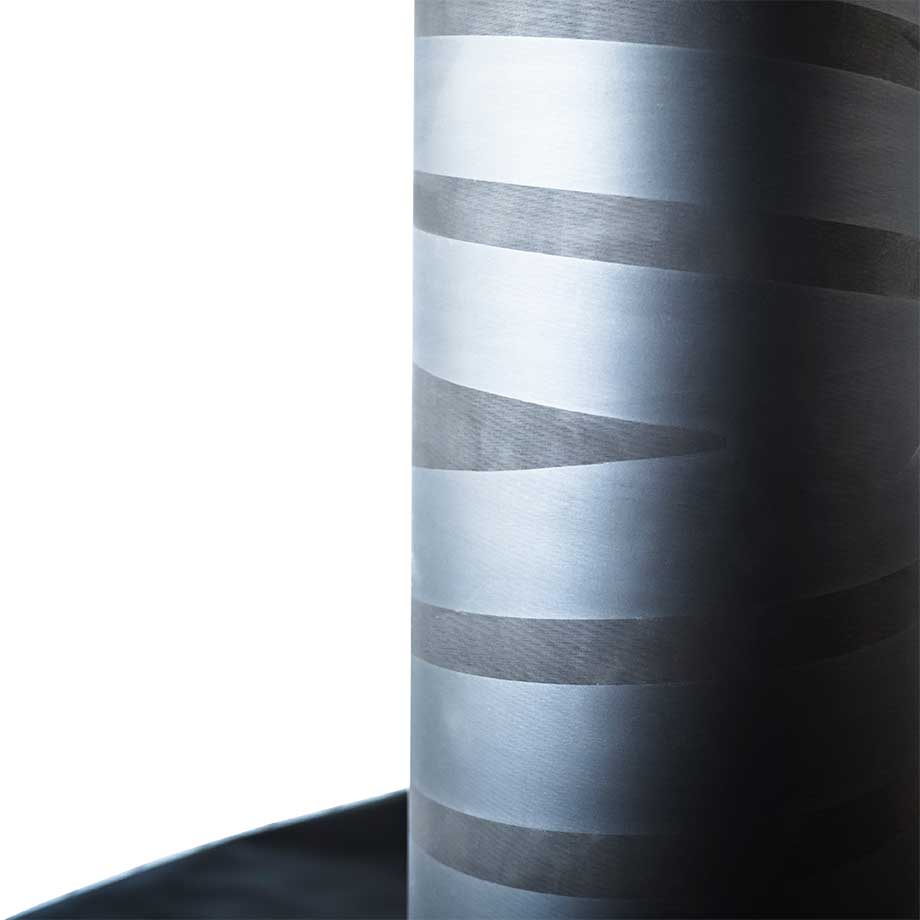
Our solution for problems with wrinkling in the process
Causes
- No sufficient heat conduction due to roll coating
- Insulation due to non-thermally conductive cover fabric
Effects
- Temperature on roll surface too high
- Chilling / heating capacity insufficient
- Process cannot be controlled exactly
Elastomer coatings generally have very poor thermal conductivity and have a correspondingly insulating effect in the process.
Thermally conductive materials enable heat to be transported in the desired direction through the roll coating. Production parameters can be controlled in a targeted manner and processes can be run more precisely and efficiently. The cooling and heating rolls used in numerous applications can thus be used effectively and provided with an elastic roll coating.
In many processes, a high thermal conductivity of the roll coating and thus a good cooling or heating performance is of decisive advantage.
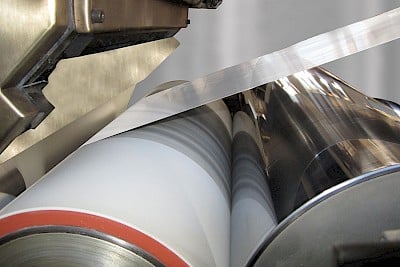
Our solution for thermal process issues
Causes
- Coating too adhesive
- No long-lasting anti-adhesiveness
- Successive build-up of adhesive residues on the cover surface
- Stickiness due to heat not dissipated
Effects
- Extruded film adheres to the take-off roll
- Damaged roll surface due to melting
- Product damage
- Short service life
- Insufficient product quality
The extrusion die is located a few centimeters in front of the pressure joint formed by the nip and take-off roll. Molten material with a temperature of up to 290° C emerges from this wide slot die. In the nip, the extruded mass solidifies until it reaches a plastic stable state. Due to the process, the temperature of the film produced in the roll gap is still very high. Therefore, the still hot film tends to adhere to the coated take-off roll. Optical and haptic properties of the extruded film are decisively determined by the surface structure of the rolls and their take-off behavior.
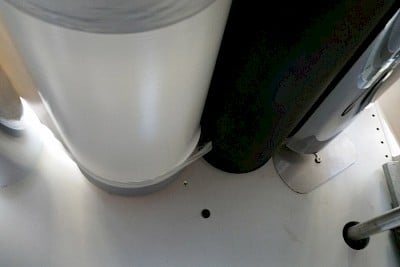
Our solution for problems with film extrusion adhesion
Causes
- Contamination due to e.g. dust, off-cuts, abrasion
- Seasonal foreign matter such as insects or pollen dust
- Particles attracted due to static charge
Effects
- Foreign bodies lead to product rejects
- Damage to the product
- Interference with downstream processes (e.g. lamination, printing, lacquering)
- Avoidable system contamination
Products that are to undergo subsequent surface finishing such as laminating, coating, lacquering or matting must have a clean surface. A high level of product purity is also required for rolled or coated products. Foreign particles from the machining processes and the surrounding air can be deposited on the product and contaminate it. In subsequent processes, these become permanently trapped in the product.
When a web is trimmed or cut, cutting residues accumulate and are dragged through the line. During rewinding, these particles can then damage the fabric itself or cause problems or rejects in subsequent converting processes (printing, coating, laminating). The same applies to dust that is attracted by static charges, insects that settle in the system or other loose contaminants. MITEX has developed a sustainable cleaning coating for this purpose.
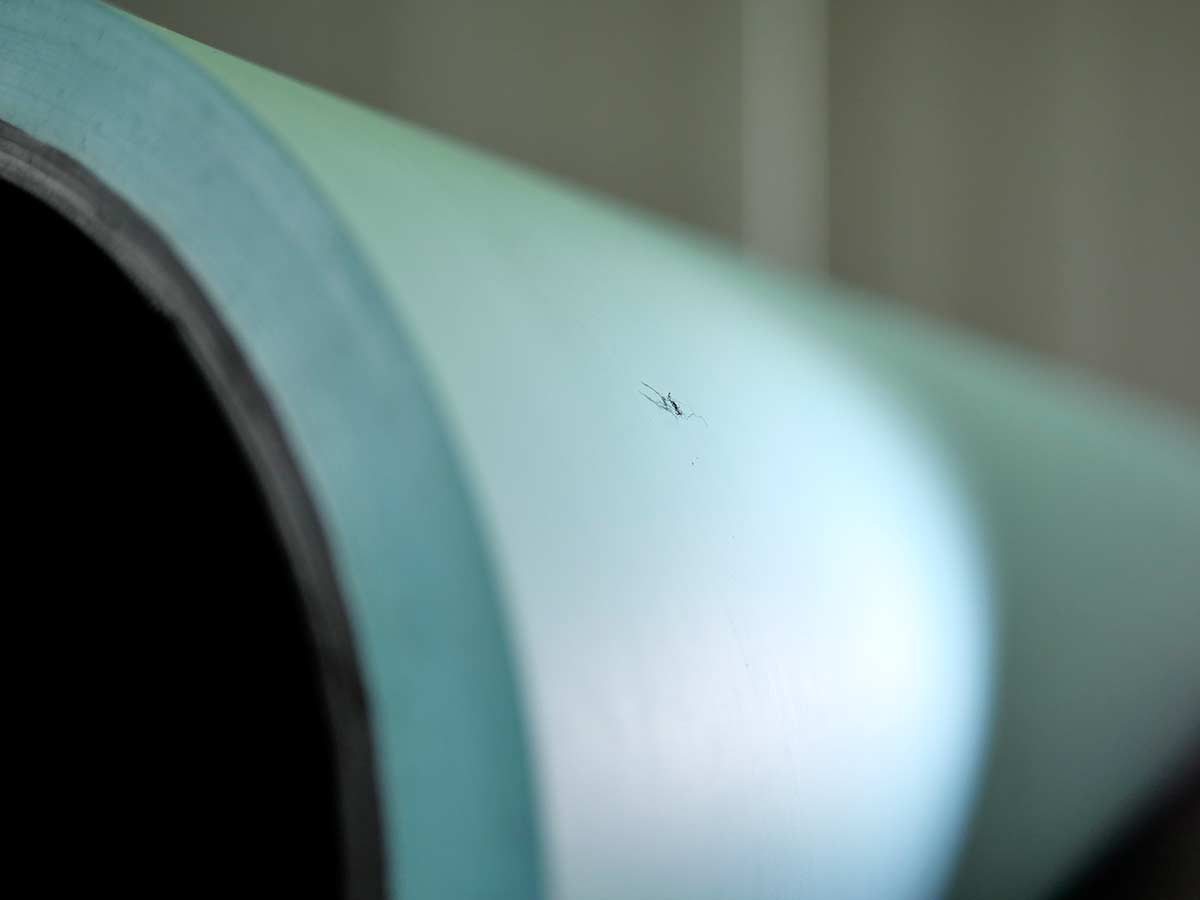
Our solution for problems with contaminated surfaces
Causes
- Non-homogeneous roll coating
- Insufficient electrical insulation
- Spark discharge through roll coating
- Mechanical and thermal overload
Effects
- Damage to the product
- Microroughness not as desired
- Wetting errors of inks / adhesives
- Loss of production capacity
To enable good adhesion of adhesives or inks to film surfaces, the surface tension must be changed depending on the substrate.
Corona treatment is used to set the desired polar or non-polar surface tension for wettability. On non-polar surfaces such as PE or PP, polar groups are generated by oxidation and the surface tension is temporarily increased. This improves the wetting properties and adhesive strength on the substrate.
As a further effect, impurities are removed from the surface and micro-roughness is increased. Optimum corona treatment requires a homogeneous, foreign body-free coating with uniform insulation properties and exact geometry that is easy to clean and allows long service lives.