Solutions for the printing industry
High requirements for roll coatings
Coated rolls are crucial for printing speed and quality. Whether flexography, gravure or offset: Regardless of the printing process, MITEX can support and realize process improvements through many years of experience with technical advice and high-performance coatings. Also in the printing industry there are many known challenges and problems which can be mitigated or eliminated by suitable roll coatings.
Below are examples of a few industry challenges with suggested solutions. For more information or a non-binding recommendation from our technicians for your application, please contact us directly.
Our rollers solve problems with:
Causes
- Use of undercut lamella spreader rolls
- Use of thinner and thinner foils
Effects
- Local overstretching of the product
- Folding in the product
Modern production machines allow the manufacture of extremely thin films at ever higher production speeds.
Conventional, undercut lamella spreaders lead to local overstretching of the sensitive substrate, which can result in wrinkling during further processing.
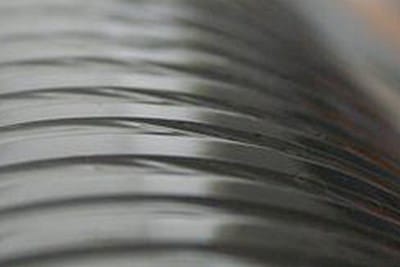
Our solution for problems with wrinkling and unsteady web run
Causes
- Use of undercut lamella spreader rolls
- Use of thinner and thinner foils
Effects
- Local overstretching of the product
- Folding in the product
Format roll coatings can lead to uneven adhesive transfer. It is often necessary to “break in” a new size roll until a good process result is achieved. The reason for this is, on the one hand, an initially poor adhesive transfer and, on the other hand, the high running resistance of new coatings, which can drive machine drives to their performance limits. MITEX offers a specially developed coating that avoids these problems.
Our solution for lamination problems
Causes
- Ink mist due to high speeds
- Contamination of the impression roller surface
Effects
- Poor expression
- Poor web guiding
- Change of electrical parameters
- Edge swelling
- Ghost printing
- Frequent cleaning
In the gravure printing unit, the high speed of the forme cylinder creates ink mist. This very fine ink mist is deposited on all surfaces. The rotating impression roller surface is particularly critical here. This can have a negative effect on the print image and damage the impression roller.
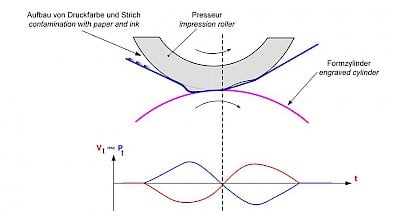
Our solution for problems with contamination of the pressurized surface
Causes
- High voltage due to charge separation between substrate and roll surface
Effects
- Explosion hazard
- High risk for equipment and operators
Due to charge separation between substrate and roll surface, high voltages can occur. The use of an electrostatic printing assist (ESA) can significantly increase this effect. One of the tasks of ESA coatings is to limit high voltages to a safe level and thus reduce the risk of fire. It is also advisable to check whether an ATEX-certified coating should be used in other comparable applications. MITEX’s technical field service will be happy to provide non-binding advice in this regard.
With ATEX certified coatings, MITEX not only sets standards and underlines the high demand for safety and quality consistency, but also makes a consistent contribution to increasing the operational safety of customers. In this respect, MITEX supports mechanical engineering as well as manufacturers of electrostatic loading and unloading systems.
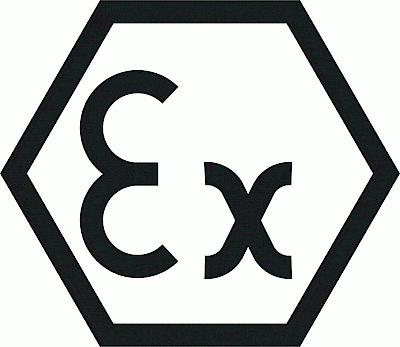
Our solution for problems with fire hazard and deflagration
Causes
- No good static charge in the substrate direction
- No good ESA effect of the cover stock
- Poor paper or ink quality
Effects
- Missing dots in printout
- Open printout
- Lack of brilliance
Modern machines in illustration, decor and packaging printing are becoming faster and faster, while at the same time the demand for print image resolution is increasing and substrate quality is decreasing.
This stands in the way of sufficient emptying of the cells and leads to poor printing results.
By means of electrostatic charging, the ink in the cell is oriented towards the substrate. This leads to quantitatively better cell emptying and thus to higher print quality.
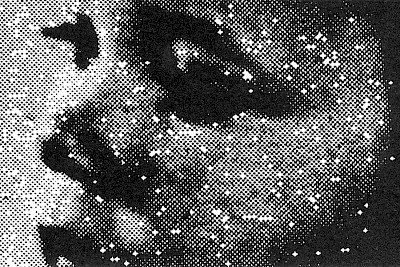