Rolls for Steel and Metal Processing
Stainless steel, steel, aluminum and non-ferrous metal applications
For the processing of steels and metals, a wide variety of high requirements are placed on roll coatings. In addition to high mechanical requirements, resistance to aggressive media and temperatures can be decisive. Special coatings for particularly demanding positions allow significant process improvements and longer service lives.
Below are examples of a few industry challenges with suggested solutions. For more information or a non-binding recommendation from our technicians for your application, please contact us directly.
Our rollers solve problems with:
Causes
- High line loads
- Hysteresis
- Core binding overload
- Rolling overheats roll coating
Effects
- Chipping from coating
- Bonding failure
- Coating sheared off
- Plant shutdowns
Bei Andrück-, Treib- und Bremsrollen kommt es häufig zu einer vorzeitigen Beschädigung des Bezugswerkstoffes in Form von abplatzenden Teilen der Rollenbeschichtung. Ursache hierfür ist ein nötiger hoher Liniendruck der Rollenposition. Bei den Rollenbezügen führt der hohe Liniendruck zu verstärktem Walken und zu einem Temperaturaufbau durch Hysterese. Der Beschichtungswerkstoff schmilzt oder überhitzt oder die Kernbindung wird extrem belastet.
Für diese Anwendungen bietet MITEX eine Reihe von hochbelastbaren Spezialbeschichtungen mit geringem Abrieb, hoher Schnittbeständigkeit und sehr guter Bindung zum Rollenkörper, die auch für sehr hohe Liniendrücke geeignet sind.
Unsere Lösung gegen hohe mechanische Belastung
Causes
- Insufficient acid resistance of the roll cover
- Solvent resistance of the roll cover too low
- Change in coating properties due to aggressive media
Effects
- Roll cover becomes cracked / brittle
- Roll cover becomes soft / sticky
- Washing out on the cover surface
- Product contamination
- Core loosening from cover fabric
Many products pass through degreasing baths, pickling and rinsing. There, dipping, deflecting, squeezing, and carrying rolls are used and guide the product through the plant segments. These rolls are in contact with the aggressive media used in these baths and become soft, sticky or cracked and the surfaces can be washed out.
Only coatings that are optimally matched to the process chemistry ensure a long service life and optimized squeezing results.
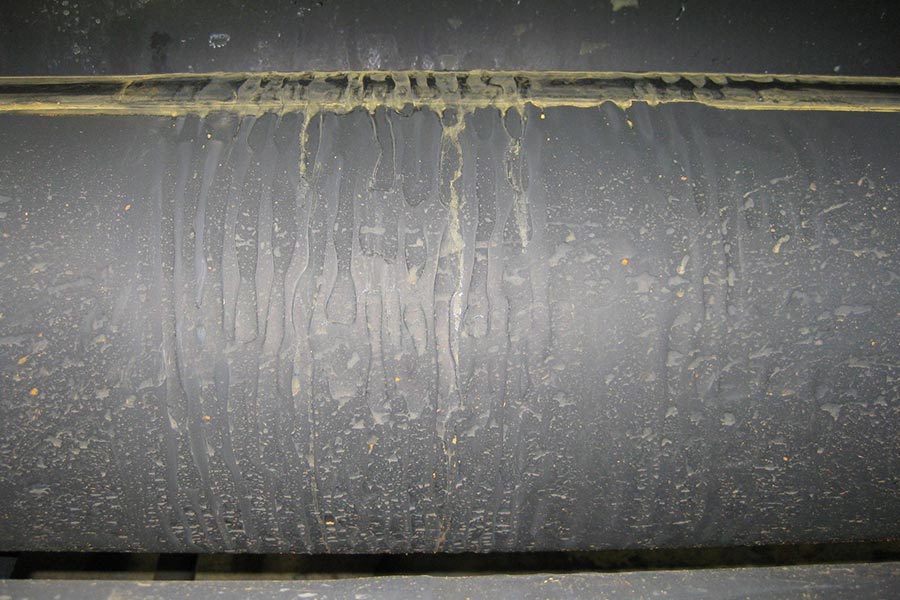
Our solutions for problems with damage due to pickling/ degreasing
Causes
- Coefficient of friction too low
- Oil or other media wetting surface
- Very high belt tension
Effects
- Slipping of the belt
- Differential speed from belt to roll
- Rapid coating wear
- Uncontrolled belt movement
S-rolls are used to control tension. This requires a very high coefficient of friction in order to be able to transfer large torques between the roller and the belt. S-rollers usually have a wrap angle >180°.
In contrast to the S-rolls, drive and brake rolls only have contact with the belt in a narrow nip.
Slipping of roll covers causes increased wear due to abrasion on the coatings. This can lead to slippage of the strip or also interfere with the control of the drives.
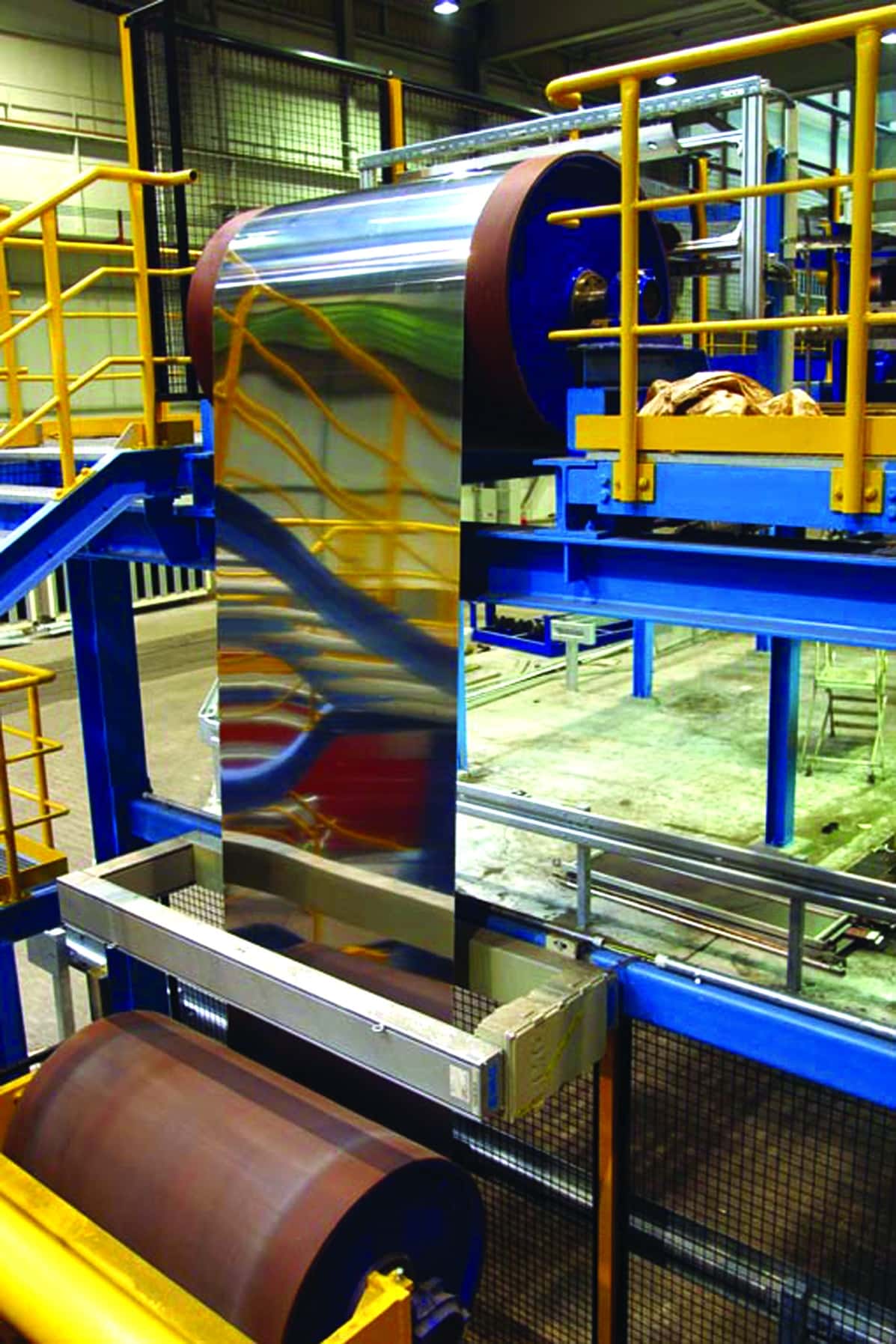
Our solution for problems with slipping due to lack of web traction
Causes
- Adhesion of the product to the roll cover
- High temperature load
- Static charge
- High contact pressure
- High production speeds
Effects
- Melting and cracks in the cover
- Wrinkles in the product
- Damaged products
- Core detachment of the cover
- Impurities in the product
The lamination of films onto steel, stainless steel or non-ferrous metal takes place at high temperatures, whereby the lamination roll coatings are subjected to high stress. Depending on the coating used, it melts, cracks or becomes slippery smooth.
High contact pressure and / or high circumferential speeds often result in damage to the lamination roll coating, for example, due to marks or detachment of the cover.
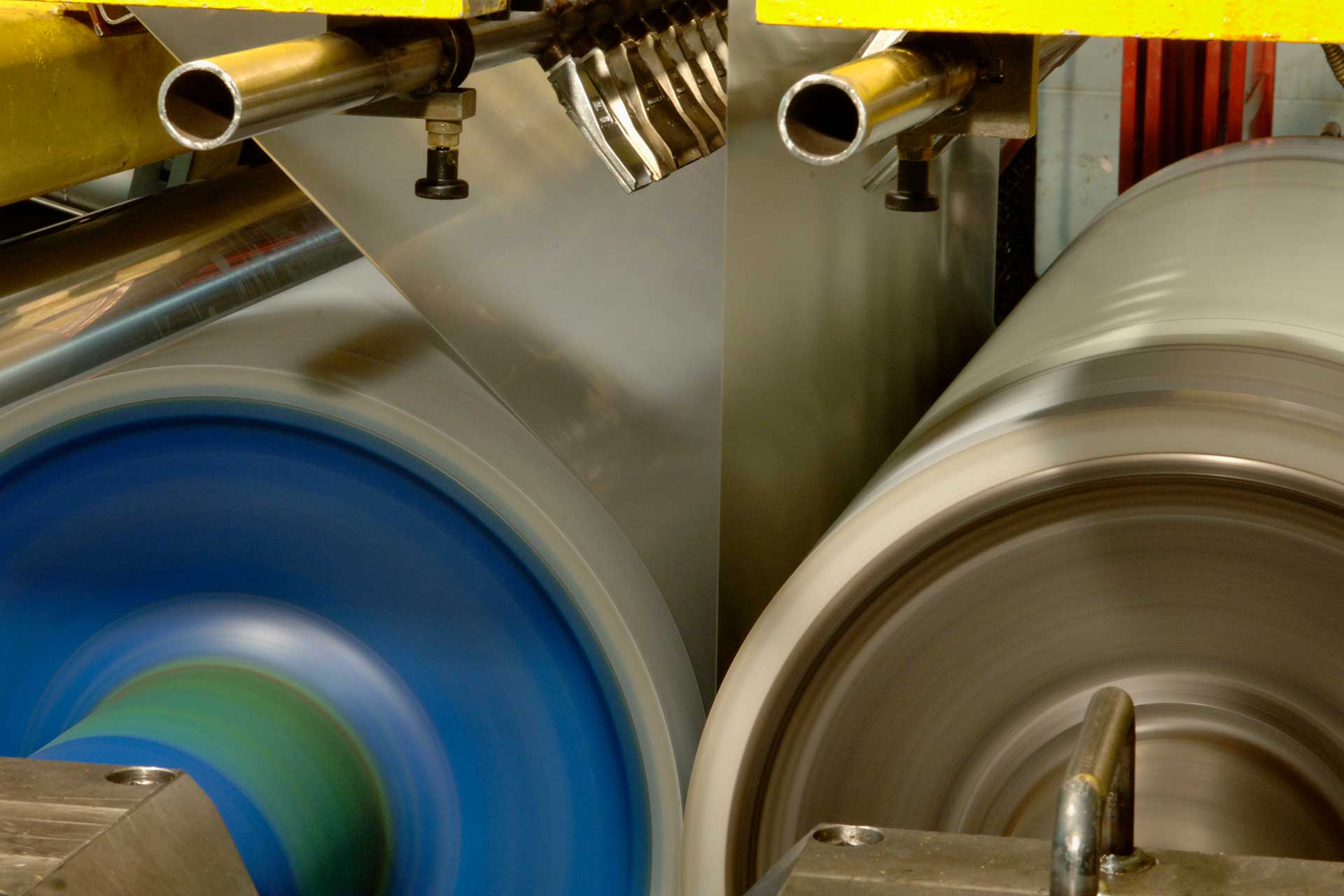
Our solution for lamination issues
Causes
- Heat transfer through hot products or media
- High process temperatures required
- Heat radiation from other plant components
- Furnace outlet or IR emitter
Effects
- Standard PUR coating melts and contaminates product
- Hardening and cracking of the cover material (rubber)
- Flattening and slippage of the cover
- Marks due to cracks and chipping of the coating
In many places, rolls coated with elastomers are subjected to high temperatures. This means temperatures between 80°C and 250°C, depending on the elastomer.
If PU coatings become too hot, they melt, rubber smooths out and cracks. The superficially melted coating material sticks to the product, is carried away and can hardly be removed.
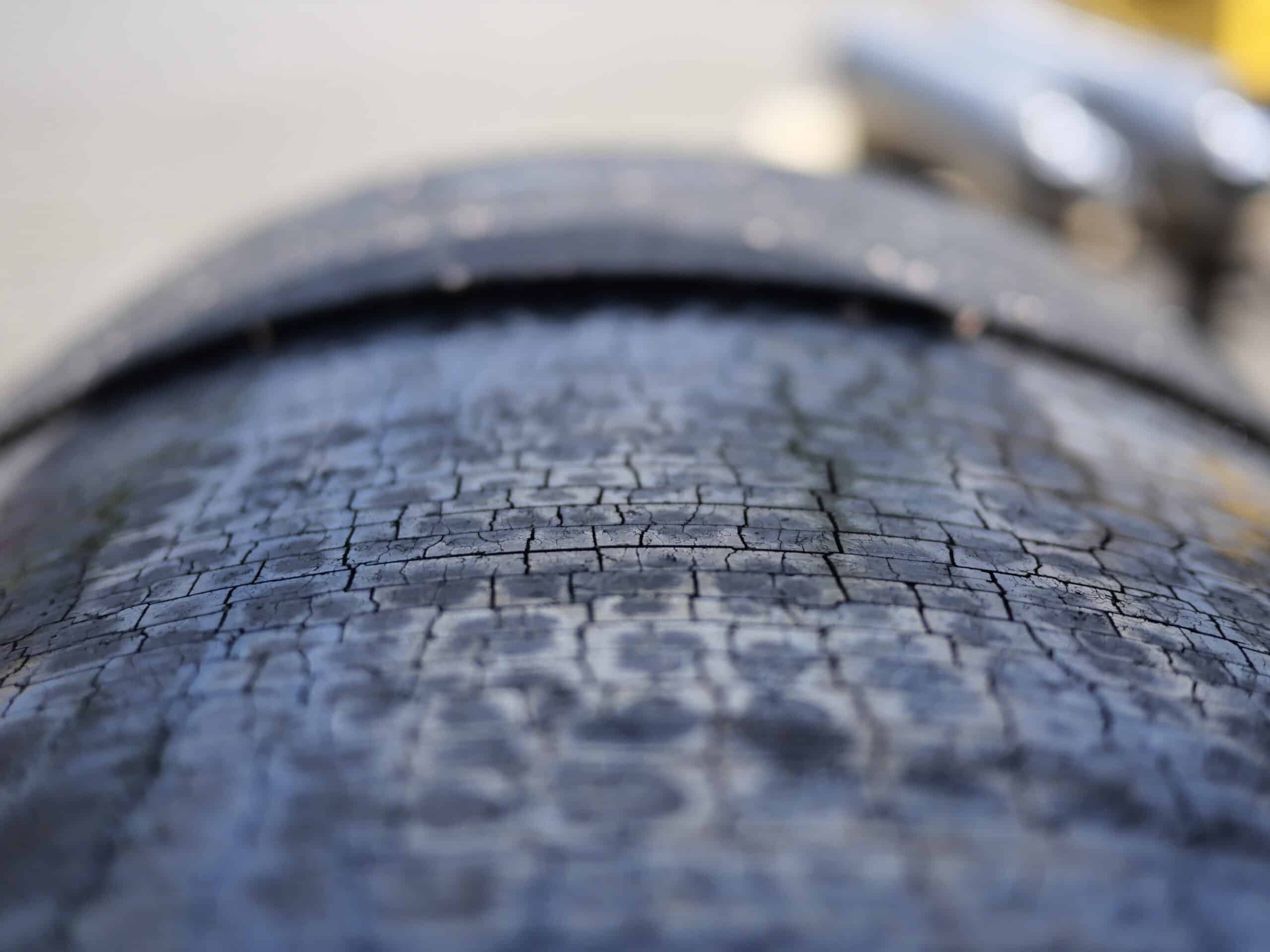
Our solution for issues with high temperature load
Causes
- Unsuitable coating
- Damage to the roll surface
- Heavily worn roll surfaces
- Attack by chemicals used
- High process temperatures
- High production speeds
Effects
- Carryover of media
- Contamination of the process chemistry
- Disturbance of the following process steps
- Drastic reduction in service life
Squeeze rolls are designed to squeeze liquid media from a substrate and seal the baths in the area of the product inlet and outlet. Minor damage to the roll surface results in local spots of residual media remaining on the belt, which then lead to unwanted effects on the end product.
If the squeeze rolls have circumferential damage or are heavily shrunk, they no longer seal sufficiently. This causes process chemicals to be carried out of the bath, which has a negative effect on subsequent process steps.
The optimum coating of a squeeze roll depends on several parameters. These include the chemicals used and their concentration, the process temperature and the product speed.
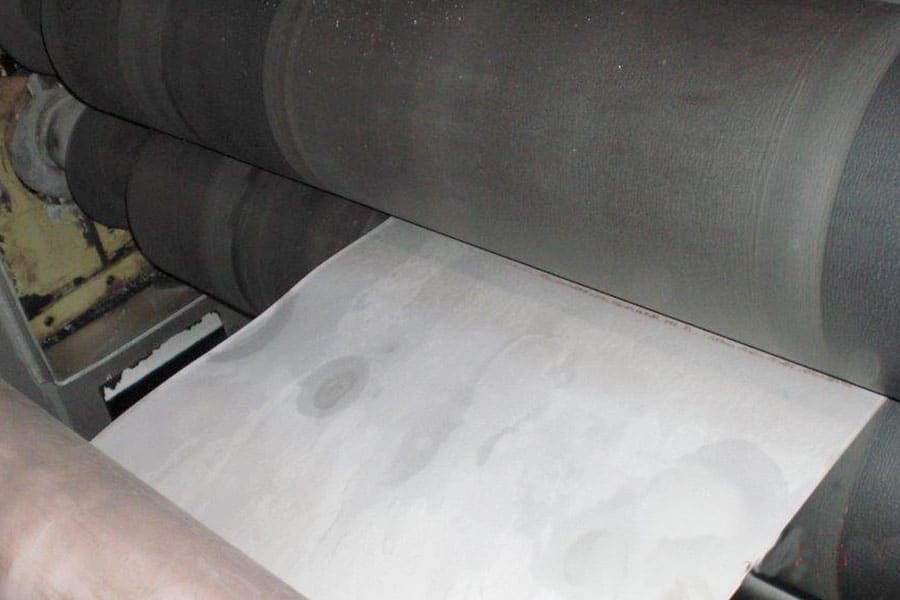