Causes
- Unsuitable coating
- Damage to the roll surface
- Heavily worn roll surfaces
- Attack by chemicals used
- High process temperatures
- High production speeds
Effects
- Carryover of media
- Contamination of the process chemistry
- Disturbance of the following process steps
- Drastic reduction in service life
Squeeze rolls are designed to squeeze liquid media from a substrate and seal the baths in the area of the product inlet and outlet. Minor damage to the roll surface results in local spots of residual media remaining on the belt, which then lead to unwanted effects on the end product.
If the squeeze rolls have circumferential damage or are heavily shrunk, they no longer seal sufficiently. This causes process chemicals to be carried out of the bath, which has a negative effect on subsequent process steps.
The optimum coating of a squeeze roll depends on several parameters. These include the chemicals used and their concentration, the process temperature and the product speed.
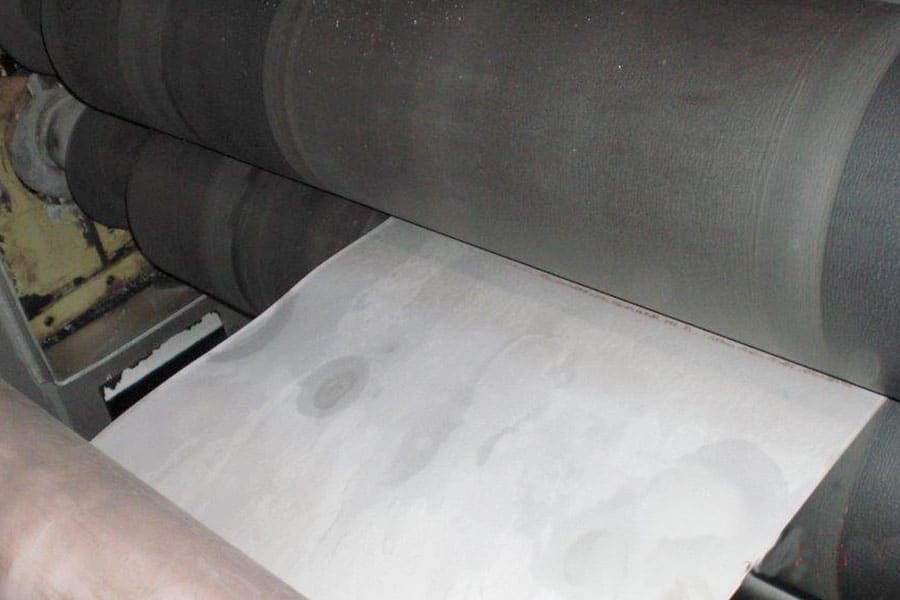