Kunststoffe, Folien & Verpackungen
Entscheidend für die Produktqualität
Walzenbeschichtungen sind entscheidend bei der Erfüllung der steigenden Anforderungen immer hochwertigerer und sensiblerer Produkte. Neben etablierten Standardlösungen für die Branche bietet MITEX Spezialbeschichtungen und individuelle Anpassungen an die Anforderungen jedes Kunden an um höchstmögliche Performance zu garantieren. MITEX Walzenbeschichtungen tragen entscheindend zur Steigerung der Produktqualität und Prozesseffizienz bei und schaffen nachweisbar einen messbaren Mehrwert für OEMs und Endanwender.
Unsere Walzen beenden Probleme mit:
Ursachen
- Unhomogene Walzenbeschichtung
- Unzureichende elektrische Isolierung
- Funkenentladung durch Walzenbezug
- Mechanische und thermische Überbelastung
Effekte
- Beschädigungen am Produkt
- Mikrorauigkeit nicht wie gewünscht
- Benetzungfehler von Farben / Klebstoffen
- Produktionsausfall
Um eine gute Haftung von Klebstoffen oder Druckfarben auf Folienoberflächen zu ermöglichen, muss die Oberflächenspannung je nach Substrat verändert werden.
Die Koronabehandlung wird eingesetzt, um die gewünschte polare oder unpolare Oberflächenspannung für die Benetzbarkeit einzustellen. Auf unpolaren Oberflächen wie PE oder PP werden durch Oxidation polare Gruppen erzeugt und die Oberflächenspannung wird vorübergehend erhöht. Dadurch werden die Benetzungseigenschaften und die Haftfestigkeit auf dem Substrat verbessert.
Als weiterer Effekt werden Verunreinigungen von der Oberfläche entfernt und die Mikrorauigkeit wird erhöht. Eine optimale Koronabehandlung erfordert eine homogene, fremdkörperfreie Beschichtung mit gleichmäßigen Isolationseigenschaften und exakter Geometrie, die leicht zu reinigen ist und lange Standzeiten ermöglicht.
Unsere Lösung für Probleme bei Koronabehandlung
Ursachen
- Verschmutzungen durch z.B. Staub, Verschnitt, Abrieb
- Saisonale Fremdkörper wie Insekten oder Pollenstaub
- Statische Aufladung zieht Partikel an
Effekte
- Fremdkörper führen zu Produktausschuss
- Beschädigungen des Produkts
- Störungen nachgeschalteter Prozesse (z.B. bei Kaschierung, Druckvorgang u.ä.)
- Vermeidbare Anlagenverschmutzungen
Produkte, die einer späteren Oberflächenveredelung wie Kaschieren, Beschichten, Laminieren oder Mattieren zugeführt werden sollen, müssen eine saubere Oberfläche aufweisen. Auch bei gewalzten oder lackierten Produkten ist eine hohe Produktreinheit erforderlich. Fremdkörper aus den Bearbeitungsprozessen und der umgebenden Luft können sich auf dem Produkt ablegen und dieses verschmutzen. In nachfolgenden Prozessen werden diese dauerhaft im Produkt eingeschlossen.
Beim Besäumen oder Schneiden einer Warenbahn fallen Schneidreste an, welche durch die Anlage geschleppt werden. Beim Aufwickeln können diese Partikel dann die Ware selbst beschädigen oder bei nachfolgenden Verarbeitungsprozessen (Drucken, Beschichten, Kaschieren) zu Problemen oder Ausschuss führen. Gleiches gilt für Staub, welcher durch statische Aufladung angezogen wird, Insekten die sich in der Anlage absetzen oder andere lose Verunreinigungen. MITEX hat hierfür eine nachhaltige Reinigungsbeschichtung entwickelt.
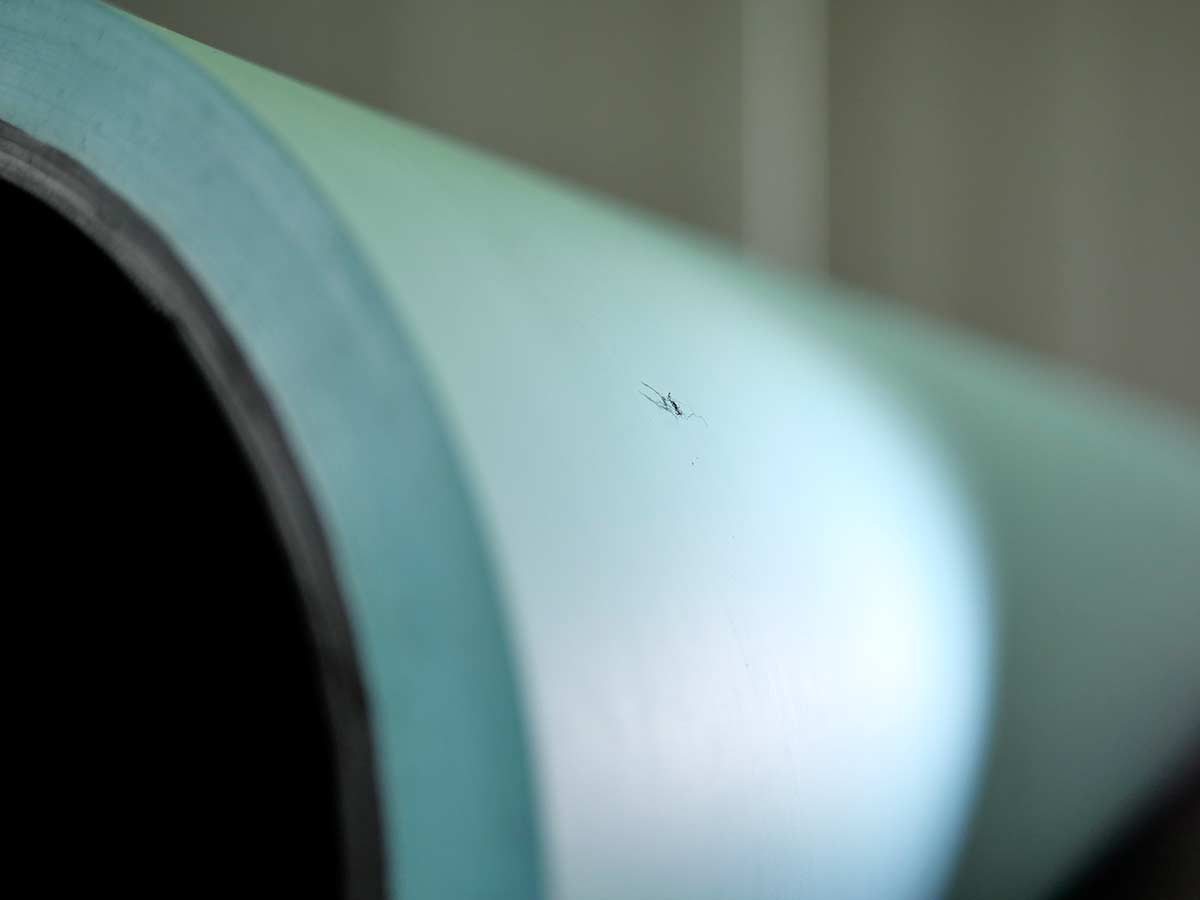
Unsere Lösung für Probleme mit verschmutzten Oberflächen
Ursachen
- Beschichtung zu adhäsiv
- Keine langanhaltende Antiadhäsivität
- Sukzessives Aufbauen von Klebstoffresten auf der Bezugsoberfläche
- Klebrigkeit durch nicht abgeführte Wärme
Effekte
- Extrudierte Folie haftet an der Abzugswalze
- Zugesetzte Walzenoberfläche durch Schmelze
- Beschädigung der Bezugsoberfläche
- Produktschäden
- Geringe Standzeiten
- Unzureichende Produktqualität
Wenige Zentimeter vor der Anpressfuge gebildet aus der Nip- und Abzugswalze befindet sich die Extrusionsdüse. Aus dieser Breitschlitzdüse tritt aufgeschmolzene Material mit einer Temperatur von bis zu 290° C aus. Im Walzenspalt erstarrt die extrudierte Masse bis zum Erreichen eines plastischen stabilen Zustands. Prozessbedingt ist die Temperatur der im Walzspalt erzeugten Folie noch sehr hoch. Daher neigt die noch heiße Folie zum Anhaften an der beschichteten Abzugswalze. Optische und haptische Eigenschaften der extrudierten Folie werden entscheidend durch die Oberflächenstruktur der Walzen und deren Abzugsverhalten bestimmt.
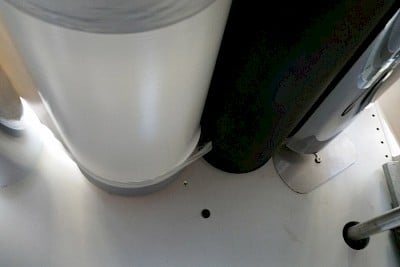
Unsere Lösung für Probleme mit Anhaftung von Folienextrusion
Ursachen
- Kein ausreichende Wärmeleitung durch Walzenbeschichtung
- Isolation durch nicht wärmeleitfähigen Bezugsstoff
Effekte
- Zu hohe Temperatur an Walzenoberfläche
- Kühl- / Heizleistung unzureichend
- Prozess kann nicht exakt gesteuert werden
Elastomerbeschichtungen haben grundsätzlich eine sehr schlechte Wärmeleitfähigkeit und wirken entsprechend isolierend im Prozess.
Thermisch leitfähige Werkstoffe ermöglichen den Wärmetransport in die gewünschte Richtung durch die Walzenbeschichtung. Produktionsparameter können gezielt gesteuert und Prozesse präziser und effizienter gefahren werden. Die in zahlreichen Anwendungen eingesetzten Kühl- und Heizwalzen können so effektiv genutzt und mit einer elastischen Walzenbeschichtung versehen werden.
In vielen Prozessen ist eine hohe Wärmeleitfähigkeit der Walzenbeschichtung und damit eine gute Kühl- bzw. Heizleistung von entscheidendem Vorteil.
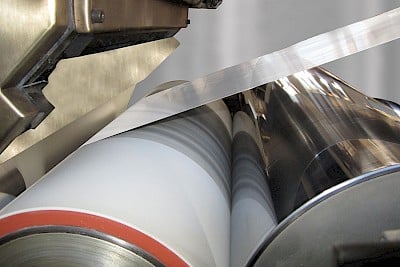
Unsere Lösung für thermische Prozessprobleme
Ursachen
- Faltenbildung durch unruhigen Bahnenlauf
- Unzureichende Breitstreckwirkung
- Lamellenbreitstrechwalze im Einsatz
- Ungleichmäßige Folienstärke
- Schwankender Bahnenzug
Effekte
- Beschädigungen des Produkts
- Ausschussproduktion
- Falten durch Überstreckung des Substrats
- Unzureichende Bahnführung
Speziell dünne Folien neigen bei der Führung durch die Anlage zur Faltenbildung was in nachfolgenden Prozessen zu Fehlern und Ausschuss führen kann. Die Ursache kann u.a. in ungleichmäßiger Folienstärke oder schwankender Bahnzugspannung begründet sein. Traditionelle Bogen- oder Lamellenbreitstrecker können bei empfindlichen Substraten zu einer Überstreckung in der Bahnmitte oder zu Markierungen auf der Folie führen.
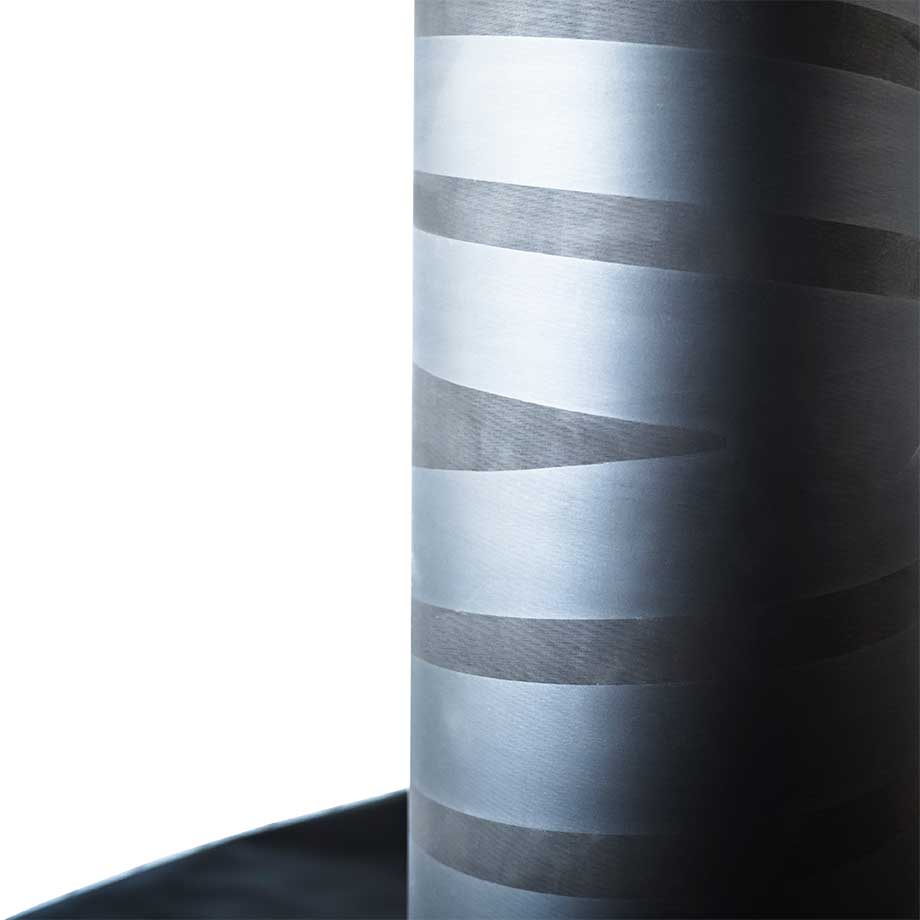
Unsere Lösung für Probleme mit Faltenbildung im Prozess
Ursachen
- Ungleichförmige Mattierung / Rauhigkeit der Vorder- oder Rückseiten von Folien
- Inhomogene optische Eigenschaften der Folien
- Falsche Rauhigkeit für die Verklebungen der Folien
Effekte
- Mindere Produktqualität
- Optisch erkennbare Inhomogenitäten
- Streifenbildung und Spots
- Produktausschuss
- Keine Prozesssicherheit
Folien in optischen Anwendungen, die z.B. als Bildschirm- oder Mobiltelefonoberflächen verwendet werden, lassen nur Inhomogenitäten zu, die vom menschlichen Auge nicht mehr aufgelöst werden können.
Technische Folien, die z.B. auf Geräten der Unterhaltungselektronik vollflächig verklebt werden, brauchen eine absolut homogene und exakt definierte Rückseitenprägung.
Die Gleichmäßigkeit der Prägung ermöglicht einen idealen Kleberauftrag und somit eine homogene starke Haftung. Auch auf der Rückseite sind nur jene Inhomogenitäten unzulässig, die vom menschlichen Auge aufgelöst werden können, da sich die matte Struktur der Rückseite bis zur Vorderseite durchformt.
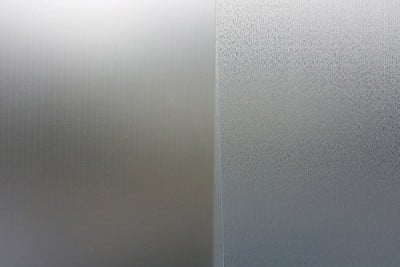
Unsere Lösung für Probleme mit unzureichender Mattierung von Folien
Ursachen
- Ablagerung von verschlepptem Klebstoffnebel
- Walzenoberfläche nicht ausreichend antiadhäsiv
- Walzenoberfläche lässt sich nicht ausreichend reinigen
Effekte
- Klebstoffaufbau auf Walzenbeschichtung
- Presseur wird am Rand der Produktbahn beschädigt
- Hierdurch einschränkung fortan möglicher Arbeitsbreiten
Beim Klebeauftrag wird Klebernebel vom Auftragswerk bis ins Kaschierwerk verschleppt. Klebereste / Klebernebel verbleiben auf der Walzenoberfläche des Kaschierpresseurs ausserhalb der Bahnbreite. Die Klebrigkeit des abgelegten Klebernebels nimmt mit der Zeit zu. In der Folge reißen kleinste Stücke aus der Beschichtung des Presseurs heraus. Dieser Effekt verstärkt sich mit der Zeit. Es können keine breiteren Produkte mehr gefahren werden.
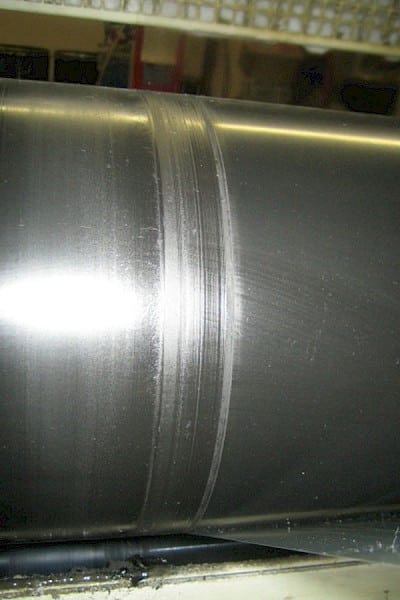